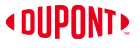
$65000 - $70000 Year
Monday to Friday
Day shift
Health insurance
Paid time off
Employee discount
Others
Job Id 235473W
At DuPont, we are working on things that matter, whether it’s providing clean water to more than a billion people on the planet, producing materials that are essential in everyday technology devices from smartphones to electric vehicles, or protecting workers in this global pandemic.
If you would like to be a part of a premier multi-industrial company that is delivering sustainable solutions that bring real purpose and value, of a company with collaborative spirit because it believes that we work best when we work together as a team and values the diversity of thought, then DuPont is the company for you!
Our Operations team is essential to delivering the innovative and life-saving products we make for our customers. We depend on our team members to actively engage in continuously improving our operations while we provide the growth and development to help them build their skills and career. Operational Excellence in our workplace unleashes the energy, creativity and collaboration – along with our tools, technology and training – that enables our people to perform at their best.
WHY JOIN US?
Our purpose is to empower the world with essential innovations to thrive. We work on things that matter!
Get to know our Purpose and make it yours by bringing innovations to market that improve the world, share a commitment to sustainability that makes our planet better and give back to communities in which we work and live.
Get to Experience a collaborative environment where teamwork is celebrated with flexibility that enhances balance and an inclusive atmosphere that is welcoming to all!
The Operations Unit Manager provides leadership and strategic direction for the safe and quality operation of one manufacturing unit at the Parlin site. The Cyrel® area consists of Cyrel® Lines 4 and 5 equipment and support systems, which is a 24/7 manufacturing unit in the Imaging Solutions section of the DuPont Electronics and Industrial Business. The team consists of approximately 60 union represented wage employees and 10 exempts including 4 first line supervisors. The successful candidate will need to maintain a strong culture of safety, teamwork, and production focus, and drives improvement.
The successful candidate will: provide leadership and direction for the area; lead improvement programs and initiatives for the area and personnel; ensure continuous and efficient production in desired quantity and quality; interface with business leadership and supply chain for coordination of schedules and understanding of customer needs; maintain accountability for establishing, forecasting, tracking and meeting fixed and variable cost objectives; set expectations for adherence to policies, procedures and safety standards; be responsible for the operation of low hazard and high hazard manufacturing processes; manage quality, cost, resources and schedules.
Specific tasks include, but are not limited to:
Directly supervising, mentoring, and developing Operations exempt employees, including First Line Supervisors responsible for shifts of shop floor operators.
Developing the area goals, improvement plans, and strategies to support Business objectives.
Interfacing with Business and other functions to develop and manage budgets that will enable achievement of Business objectives. Forecast, monitor and control area budgets. Drive and track cost saving improvements.
Setting expectations and holding people accountable to core value compliance (EHS/PSM, Ethics, & Respect for People) and modeling appropriate behavior.
Working closely with Maintenance, Supply Chain, Engineering Sciences, Quality, Human Resources, Environmental, Health and Safety (EHS) and Site Support personnel to maintain alignment and teamwork in executing manufacturing responsibilities.
Using/gaining proficiency in SAP manufacturing software including capacity planning, cost center management, and other functions in SAP.
Working with site leadership and HR to drive collective bargaining improvements, alignment, and negotiations with shop floor represented personnel.
Developing and executing periodic professional communications with Supply Chain and business leadership including updates and presentations.
Maintaining Responsibility for the oversight of onsite logistics and warehousing contractors. Interfacing with Contract Management personnel at the site and business levels to drive improved contractor performance.
Orchestrating the daily and weekly communication rituals of the operating areas, to ensure seamless communication and teamwork across a diverse organization.
Driving Standard Practice alignment.
Prioritizing and monitoring the Key Performance Indicators (KPIs), including TEEP/OEE, yield, Production to Plan.
Ensuring Process Safety Management (PSM), ISO9001-2015 (Quality Management Systems), ISO14001 (Environmental) compliance for the area.
Working closely with Capital Engineering to ensure projects are prioritized, planned, integrated, and coordinated for safe and efficient quality execution to meet the business needs.
Developing Succession Planning - Maintaining appropriate levels of competency and qualification for employee shop floor proficiency.
Instituting requirements for training and proactive development of employees.
Reaffirming roles and responsibilities of direct reports and holding them accountable for their performance.
Utilizing Six Sigma tools to improve manufacturing processes.
Providing leadership, direction, and oversight to area Maintenance Coordinators to ensure the Work Management Process is functioning optimally and maintenance Work Orders are detailed, accurate, and prioritized.
Requirements
Education: minimum BS degree in Engineering. Chemical, Mechanical, Electrical preferred.]
Industrial experience: 10+ years’ experience in chemical or discrete manufacturing production environments
5+ years of leadership experience
Demonstrated leadership, collaboration, and communication skills.
Demonstrated capability to quickly understand technology and drive / support change.
Demonstrated commitment to diversity, equity & inclusion.
Proven ability to lead cultural changes and create winning teams.
Is data driven, action oriented and works with a sense of urgency.
Fluency in English is required.
Preferred Qualifications
Experience with process safety management and life saving skills.
Experience with Industry 4.0 as well as Lean Six Sigma methodologies and applicable digital tools to drive Operational Excellence
Good knowledge of budgeting and resource allocation procedures to ensure strong financial rigor and accountability.
Experience supervising and mentoring people.
Communication
Leadership
Teamwork
Others
5 years
10+ years
Others
Business administration
On going position
General Location, within a limited area